Need to Eliminate Maintenance Downtime?
Reduce Downtime with Data
Equipment reliability is the key to efficient production and profitability. Unplanned downtime due to equipment failure often results in a snowball effect of lost production and massive costs. Tracking downtime and understanding its cause sheds light on what steps need to be taken to get breakdowns and downtime under control. COGZ Downtime module gives you the data you need to develop proactive maintenance strategies to keep your downtime in check.
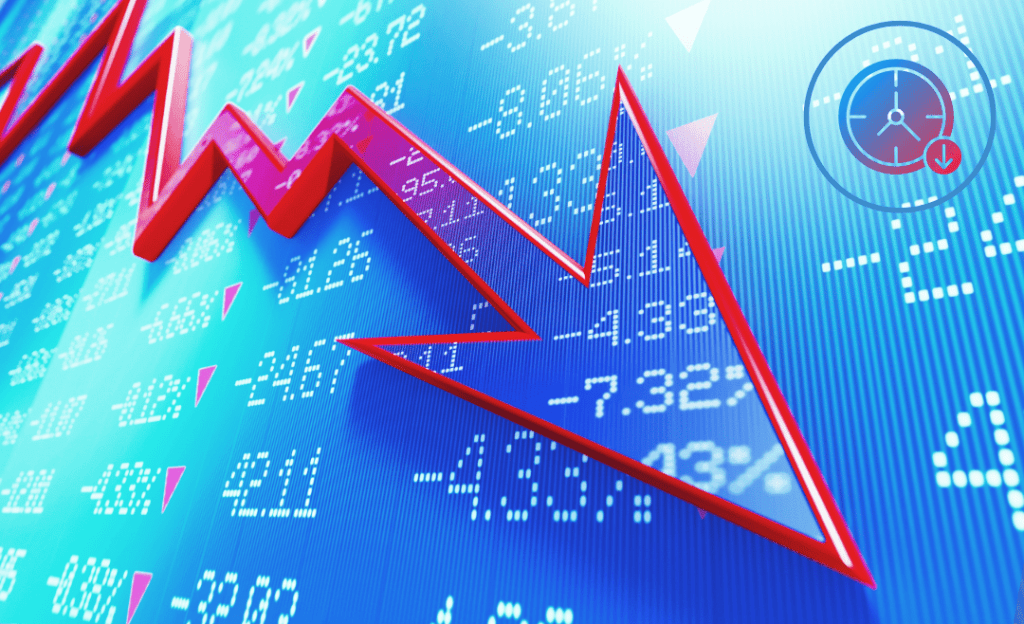
COGZ Helps Track Downtime
Easily Enter Downtime
Enter downtime on the Downtime Form when closing work orders or from the Equipment Menu. Document the reason the equipment was down and the required repairs. Choose from six customizable downtime categories for reporting purposes. View and analyze the downtime data you have entered on the Downtime List and Downtime Report.
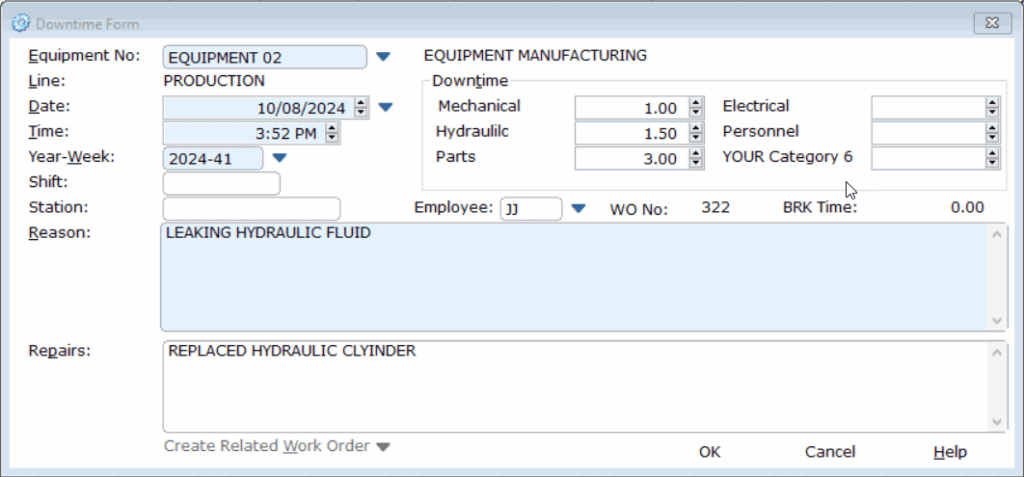
Downtime Report
Use the data you have collected to see which equipment has the most downtime and what your leading causes of downtime are. The Downtime Report offers an in-depth analysis of all downtime entries. See both work order time by category and total equipment downtime. Also, included is a summary of downtime by line. The Downtime report allows you to:
- Maximize production by improving response time.
- Reduce costs by prioritizing efforts in the areas with the most costly downtime.
- Increase productivity and reliability as unscheduled downtimes are eliminated.
Downtime for a specific piece of equipment may also be viewed on the Downtime tab of the Equipment List. High levels of downtime on a piece of equipment may be a sign that the equipment should be replaced or that preventive maintenance schedules should be revamped.
COGZ Dashboard Visualizes Your Downtime Data
COGZ Dashboard allows you to customize a downtime goal and track your progress. The Dashboard shows a snapshot of your downtime status for the current week. Easily drill down to a more detailed view to specify a different time period. Also view downtime by category and by equipment.
Discover which equipment has the highest levels of downtime. Focus your maintenance efforts on the areas that will make the largest impact. COGZ gives you the data you need to make educated decisions that will optimize the productivity and profitability of your entire operation.
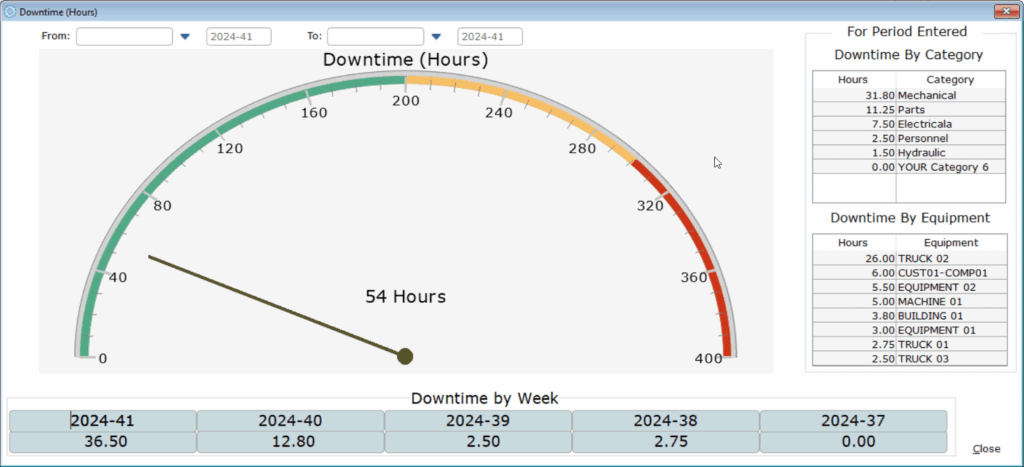
Work Order Availability Report
The Work Order Availability Report makes tracking statistical information simple. The report calculates Mean Time to Repair (MTTR), Mean Time Between Failure (MTBF), and Equipment Availability based on the timing of work orders scheduled and completed. Uncover areas for improvement and enhance the effectiveness of your maintenance program with these KPIs.
COGZ Downtime Module Makes Data Driven Decisions Easy
Reducing equipment downtime can be challenging. COGZ Downtime Module simplifies downtime analysis by summarizing your downtime data and providing details when needed. Our visual displays allow you to set goals and empowers you to make informed decisions. Easily identify areas that need improvement and implement solutions quickly. COGZ Downtime Module will help you use your data to optimize your entire maintenance department.