Maintenance Software for Manufacturing Facilities
- Manufacturing Maintenance Software boosts production output and controls overhead costs in your manufacturing facility
- Optimize your entire maintenance operation
- Extend asset lifespans and improve uptime
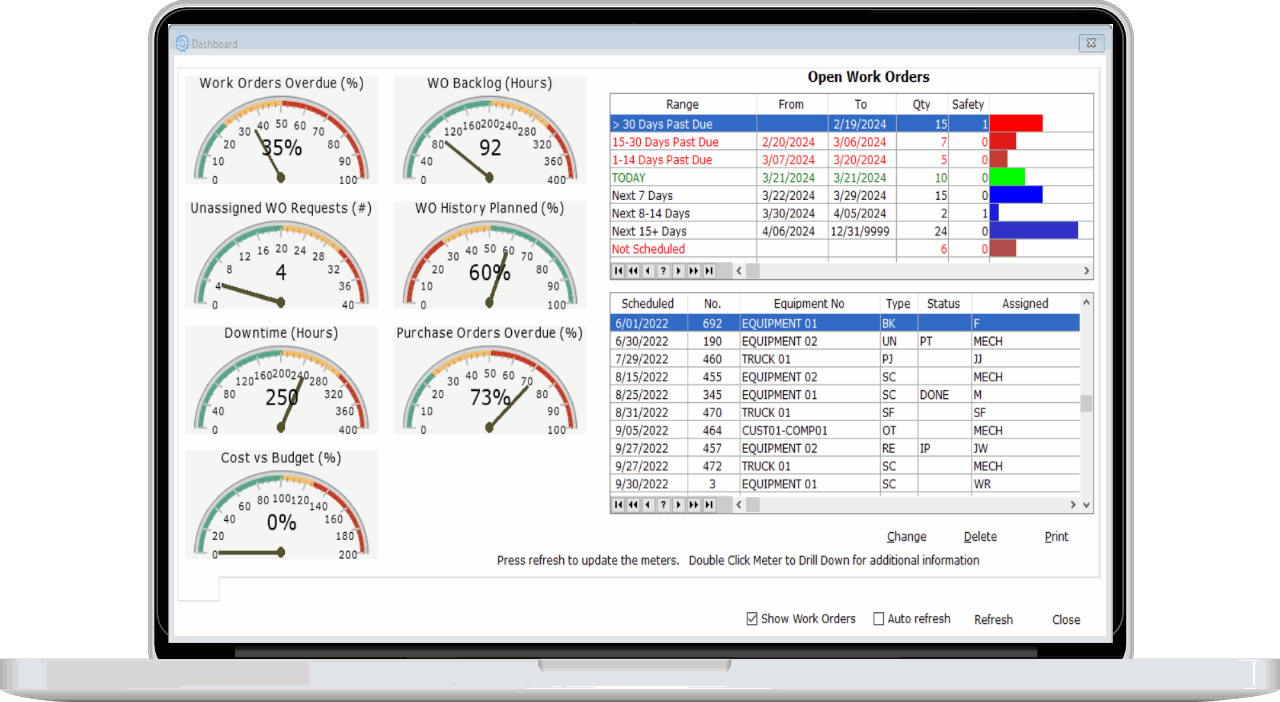
Top CMMS for Manufacturing Facilities
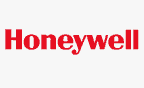
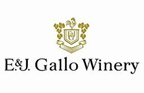
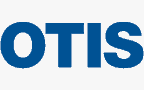
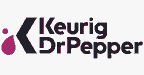

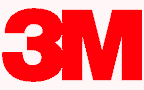
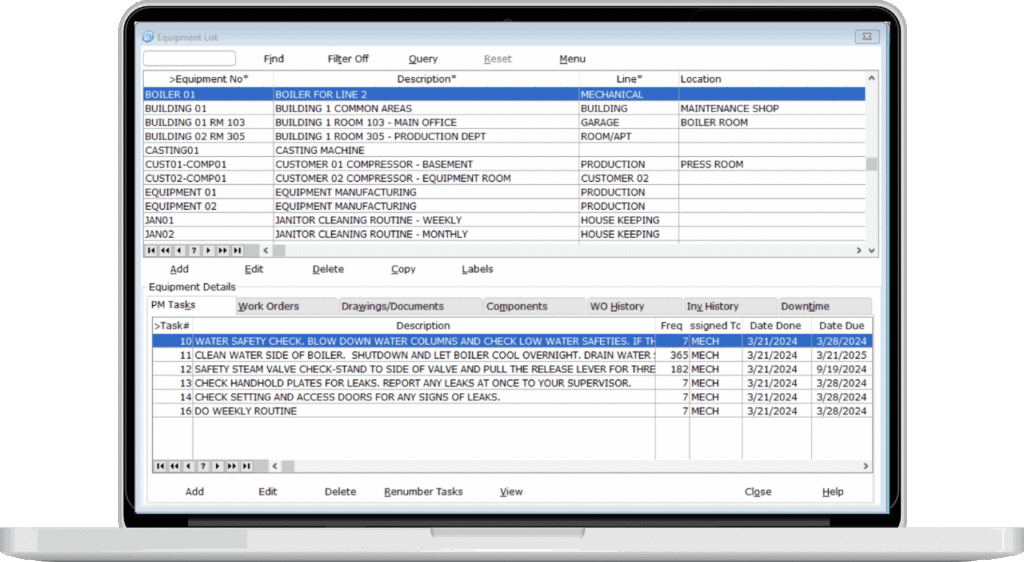
Keep Downtime in Check!
Track and Prevent Downtime
Automate Preventive Maintenance
Fast Track Return on Investment
Track Progress in Real Time
Optimize Asset Performance/Lifespan
Improve response times
Keep Inventory in Stock
Drive Productivity and Improve Efficiency with CMMS
%
Increase In Productivty
%
Increase In Efficiency
%
Decrease in Downtime
%
Decrease in Unplanned Work
Automatically Schedule Recurring Tasks
Maintenance Software for Manufacturing Facilities is a comprehensive maintenance tool that schedules preventive maintenance, tracks work orders, manages inventory and streamlines purchasing. Manufacturing CMMS is a powerful system that manages all of your maintenance activities including inspections, work orders, and requests. Additional features include cost and downtime tracking, work order requests and host of other features. Increase production and cut maintenance costs by reducing breakdowns and expensive downtime. Increase efficiency with easy setup and all the information you need on one screen. We have helped thousands of manufacturing companies optimize their maintenance departments.
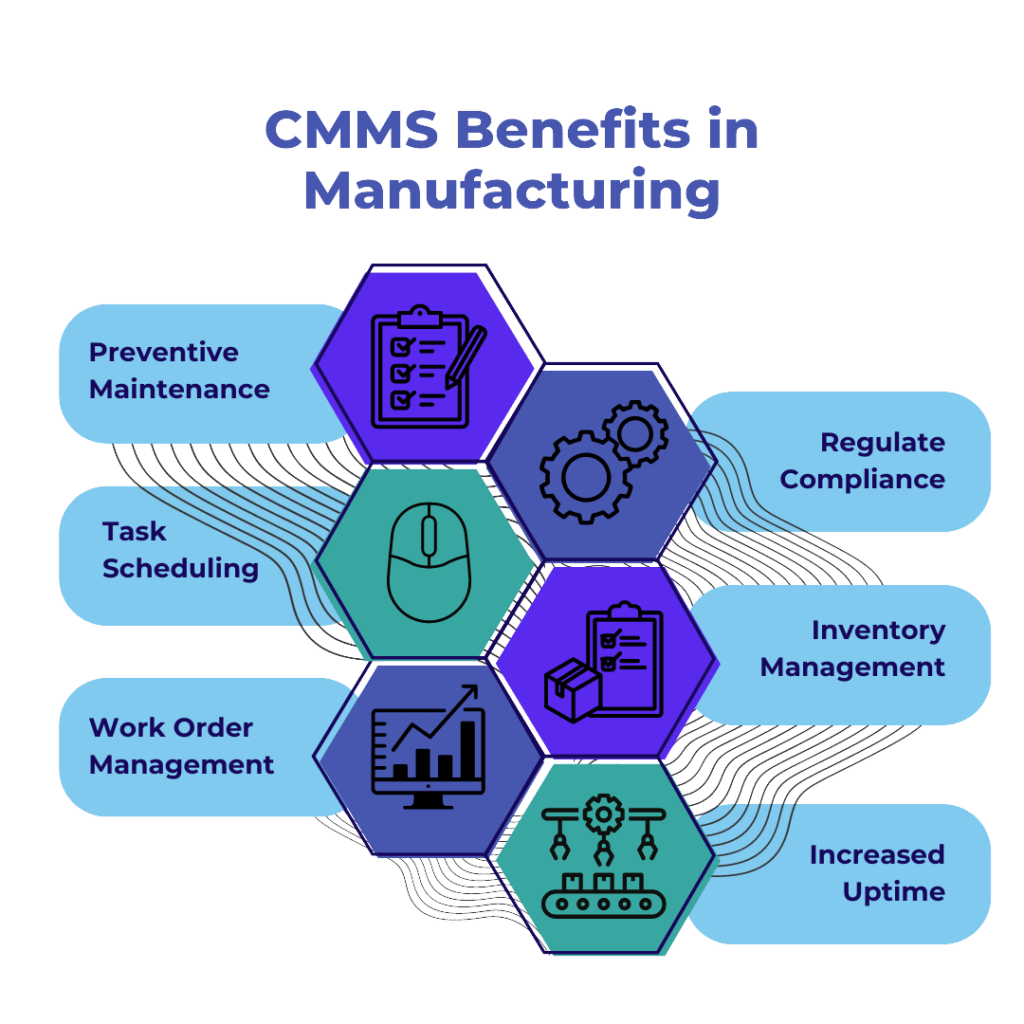
An All in One Manufacturing Solution
Centralized Paperless Record keeping
Centralize and share your maintenance data with safe, secure and reliable CMMS Software.
Mobile Maintenance Management
Perform and track maintenance on the go and in real time. Easily find the information you need to get the job done.
Purchase Order Management
Streamline Purchasing with COGZ CMMS. Automatically re-order inventory when quantities fall below the minimum required.
Full Maintenance Automation
From preventive maintenance to automatic inventory re-ordering CMMS returns time to you.
Manage Resources and Labor
Maximize efficiency by balancing workloads. Know what parts you have on hand and locate them with ease.
Easy to Use Interface
COGZ allows you to enter data on the fly to speed up implementation. Rapidly find the information you need with our easy to navigate lists.
Integrated Reporting
Make confident business decisions with customizable data exports and reporting.
Streamline Work Order Management
Plan and prioritize work orders. Automate Work Order Requests. View Work Order Status and aging. Track and report Downtime.
Notifications
Receive notifications via email or text message when new Work Orders and Work Order Requests are Created or when work is done.
CMMS Software for Manufacturing Reviews
Read about COGZ User Experiences
Improve Equipment Reliability and Maximize Production
Manufacturing plants are high speed and high stakes environments. Processes are interrelated and when equipment breaks down there is a snowball effect. This coupled with the large volume and wide variety of specialized equipment make the job of managing maintenance in the manufacturing industry extremely difficult.
Equipment is costly to purchase and to maintain. The parts utilized are unique and can be difficult to find. Downtime is particularly costly. Bottom line, performing maintenance effectively is a real challenge.
Manufacturing and industrial facilities require a more comprehensive Maintenance Software to meet their specific needs. With such a high volume of specialized equipment the need for tracking equipment history, inventory, and drawings is critical. The ability to efficiently schedule preventive maintenance to minimize the amount of times you have to shut down a machine is equally important.
Manufacturing maintenance software is designed to excel in a manufacturing environment with powerful features that meet these requirements. We have helped thousands of manufacturing operations effectively manage their maintenance departments. See our article on Five Ways Maintenance Planning with COGZ can increase your productivity.
Manufacturing Industry Challenges
The manufacturing industry is facing a host of new challenges in today’s economy. The industry as a whole is evolving to address these difficulties. Individual companies will be forced to evolve as well if they hope to thrive in this changing environment. Effective planning and flexibility has become crucial to surviving the rapidly changing conditions of the global economy. Manufacturing Maintenance Software can help maintenance teams adapt. The biggest challenges facing the manufacturing industry today are:
- Shifts in Demand – It is difficult to keep production up to meet increases in demand as well as new demand for different products. Manufacturing Maintenance Software keeps equipment running smoothly and consistently, maximizing productivity and product quality.
- Rising Costs and Lower Profit Margins – Inflation and supply shortages have driven costs to all time highs, making it difficult to achieve acceptable levels of profitability.
- Workforce Shortages – A shortage of employees has made it a challenge to meet production goals.
- Supply Chain Disruptions – Limited availability of parts and raw materials have made it tough to keep equipment up and running and producing products.
- Cybersecurity Risks – Cyber threats such as data breaches and ransomware attacks have required manufacturing facilities to take new security precautions to ensure that their valuable data is safe.
- Emphasis on Safety – The pandemic brought new focus to worker safety in manufacturing plants. Safety measures must be performed and tracked to avoid future production interruptions.
Improve Maintenance Reaction Times
The manufacturing industry has been forced to evolve to adapt to the new challenges facing their industry. Demand for products continues to rise. The result is a need to increase production levels with a lower numbers of employees available to perform the work. The industry has taken the following measures to meet demand while remaining profitable.
Rise in Automation – Increases in demand coupled with workforce shortages has forced the industry to implement even more automation to keep productivity high. Automation saves long term costs and increases production levels. Maintenance requirements will increase with the addition of more complex machinery.
Adoption of Smart Technology – Internet connected machinery allows close monitoring of manufacturing processes. This allows for identification of opportunities to optimize efficiency. Data analytics is used to improve processes.
Retain Skilled Workers – With workforce shortages and the great resignation it has become crucial to keep skilled workers. Creating a favorable company culture, reducing stress on employees, and providing continuous learning and growth opportunities are some ways that skilled employees can be enticed to stay at your company.
Beat Supply Chain Challenges – Locating and ordering parts has become difficult and expensive. Data analytics is being used to manage supply chain disruptions.
Move toward Predictive Processes – Predictive Maintenance is being used to streamline manufacturing processes. Equipment is monitored and data is collected to predict when they will fail. Maintenance can then be performed prior to the predicted failure. This approach has been proven to reduce unplanned downtime, cutting costs and increasing productivity. Maintenance Software for Manufacturing can help gather the data needed to implement these processes.

Benefits of Manufacturing Maintenance Software
Are you trying to help your maintenance department adapt to today’s manufacturing industry challenges? See how Maintenance Software for Manufacturing and Industrial Operations can help.
- Increase Production – Performing timely preventive maintenance reduces unplanned maintenance and downtime. Get organized and make the most of the resources you already have. Increasing efficiency allows you to get more done.
- Cut maintenance costs – Shifting focus to preventive maintenance saves money. Preventive tasks will always cost less than fixing a breakdown. Right size your maintenance schedule with data analysis. Avoid performing more maintenance than necessary. Lower costs mean higher profits.
- Supports Employee Retention – Take the stress off your maintenance technicians. Increase wrench time by decreasing the amount of time spent traveling and looking for information. Increasing efficiency helps to lighten their workload.
- Robust Inventory Management – Keeps the parts you need in stock. Avoid backorders and expensive overnight freight with proper inventory management. Control inventory expenditures with precise inventory tracking.
- Keeps your Data Secure – Cloud Hosting provides an additional layer of security for your valuable data. Backups are performed frequently with offline and offsite redundancy. Rest assured that your data is safe no matter what happens in your facility.
- Ensures Safety Protocols are Performed – Safety work orders make sure that safety procedures are performed consistently and documented.
- Move to Predictive Maintenance – Collect data every time maintenance is performed. Managers can use data analytics to move to a predictive maintenance schedule. Scheduled maintenance can be reduced due to the precise nature of predictive maintenance schedules.